Blog
Blog>
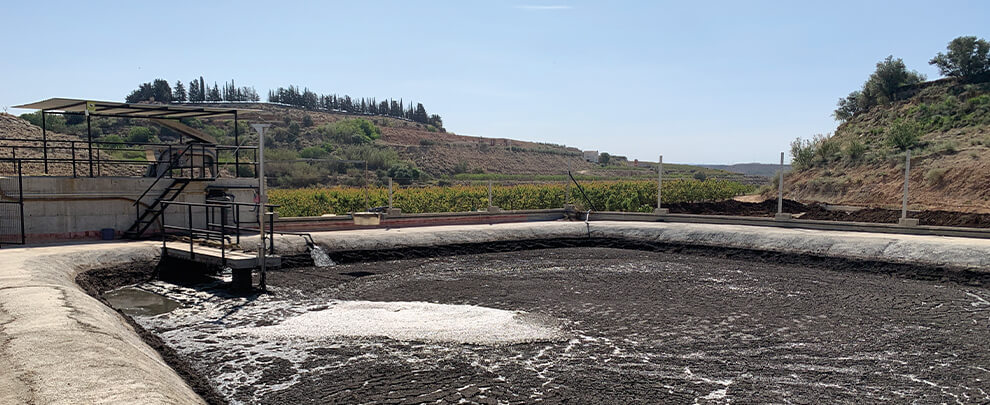
How to mitigate the smell of pig farming
26th November 2024 - News
Óscar Toledano. Rotecna Sales Manager.
Foul odours perceived in the vicinity of our farms and when fertilising the fields with slurry and its by-products are some of the main complaints we receive as a sector. In extreme cases, they become a problem that compromises the viability of the activity. For this reason, it is essential to know what methods and techniques we have at our disposal to mitigate them and thus reduce the impact of our activity and the rejection it can generate.
The foul smell of pig slurry (a mixture of faeces and urine with remains of water and food) is due to various substances resulting from the decomposition of organic matter and the metabolic processes of the microorganisms in the slurry. The main substances responsible for foul odour are:
- Ammonia (NH³) comes from the decomposition of nitrogenous compounds, mainly urea, in urine. It has a pungent and intense smell.
- Volatile fatty acids(VFAs), produced during the anaerobic fermentation of carbohydrates and fats: acetic acid with a vinegary odour, butyric acid with a rancid aroma, sour and spicy propionic acid, etc.
- Hydrogen sulfide(H²S), caused by the anaerobic decomposition of organic matter containing sulfur. The smell of rotten eggs.
- Methyl mercaptan(CH³SH), generated during protein degradation, contains sulfur. It has a particularly vile and nauseating odour.
- Dimethyl sulfide(DMS) and dimethyl disulfide (DMDS) are emitted during protein degradation and contain sulfur. Smelling like cabbage or rotten vegetables.
- Idols and eschatology detached when amino acids degrade, especially tryptophan. Typical faecal and tar odour.
- Phenols and cresols are created during the degradation of phenolic compounds. Phenolic odour and sometimes tar-like.
- Volatile amides, such as cadaverine and putrescine, are produced by the breakdown of amino acids and smell like rotting meat.
- Organic volatiles(VOCs) caused by various degradation and fermentation processes. Alcohols have sweet aromas, and ketones smell like fermented fruit.
Each of these substances contributes to pig slurry's characteristic and unpleasant smell, and the combined implementation of appropriate management and treatment strategies can help significantly reduce such odours.
The first action that can be carried out to mitigate and control these odours is to implement strategies during the manufacture of feed to optimise the assimilation of nutrients by animals to reduce the excretion of the substances that cause them or minimise their emission into the environment. Some of these strategies are:
- Adjust the grind of each feed component to optimise particle size and digestive efficiency.
- Apply a multiphase diet, dispensing different types of food throughout the life of the animals and adjusting the nutrient contribution of the feed to the animal's needs in each growth phase.
- To enable efficient protein synthesis and decrease the excretion of unnecessary amino acids such as urea, it is advisable to supplement the diet with essential aminoacids, including lysine, that may be limiting for this process.
- Use enzymes such as phosphatases and proteases that help improve digestive efficiency and nutrient absorption.
- Use probiotics or prebiotics that strengthen the intestinal flora of the animals.
- Reduce the use of sulfur compounds, such as sulfates.
- Decrease the electrolyte balance of the diet by using acidifying salts to lower urine pH. This helps reduce ammonia emissions as low pH favours the ammonium form, which remains dissolved in the slurry. Likewise, the acidic pH inhibits the action of some microorganisms and processes that generate foul-smelling gases.
- Use fermentable fibre sources that encourage nitrogen to be excreted via faeces instead of urine, making it less susceptible to breaking down into ammonium than urea in urine. In addition, these sources of fibre also promote the production of volatile fatty acids, which contribute to reducing the pH of the stool.
- Use additives that capture the compounds that cause odours, such as cassava, quillay, zeolite or sepiolite.
Slurry should be distributed as close to the ground as possible. Photo: Rotecna.
The next area where we can take action is inside the warehouses. Once the slurry reaches the pits, the decomposition of organic matter begins, leading to the generation of odorous compounds such as ammonia and volatile fatty acids. Some of the main techniques we can apply in this phase are the ones we have already discussed in other articles where we have dealt with the issue of reducing greenhouse gas emissions and environmental pollutants such as ammonia. It should be noted that the reduction of emissions inside the warehouses will also have a very positive impact on the health of the animals and their performance:
- Minimise feed waste using efficient feeders and drinkers installed in the appropriate place and correctly adjusted. Do not encourage competition by putting more animals than recommended per feeder.
- Maximise the average daily gain of the animals, keeping them in their environmental comfort zone.
- Use efficient and reliable feed distribution systems, which minimise losses due to breakdowns and allow the animals in each room or pen to be fed with different types of feed instead of all eating the same type, regardless of their specific requirements by size or gender.
- Keep animals and surfaces dry and clean. To this end, it is vital to respect the optimal densities for each type of animal and an appropriate design of the facilities, both in terms of the distribution of space and the placement of elements such as feeders and drinkers, as well as adequate environmental control. In the case of using dry litter instead of grids and pits, aerobic conditions should be encouraged since the lack of oxygen in the litter promotes the activity of anaerobic microorganisms that produce foul-smelling compounds.
- Remove the slurry from the warehouse as often as possible to reduce the amount of gases produced and not keep it in the pit for more than seven days. As we need a minimum height of 10 to 15 cm of slurry to be able to evacuate it by gravity through pipes, we can use partially grated floors, collection trays under the grates or V-shaped pits to achieve that height with less volume or even with vacuum suction equipment. Alternatively, we can implement on-site separation systems, allowing urine and water to drain constantly, and, using scraper systems, frequently drag solid faeces out of the house. Water trawling systems can also be used, but they are not recommended if it is a limiting factor. In addition, these systems increase the volume of slurry produced and the cost of its subsequent handling. However, it must be deemed that the slurry's dilution reduces its production of foul odours.
- The greater contact area of the slurry with the air and the currents on this surface encourages the production of odours, so we must minimise them: on the one hand, we can use partially grated pits or V-pits and, on the other hand, reduce the flow and speed of the air on the surface of the slurry using appropriate ventilation systems.
- High temperatures speed up microbial activity and the volatilisation of foul-smelling compounds, so high temperatures should be avoided. This is why an excellent environmental control system is essential. Slurry cooling systems can be installed in the pit, taking advantage of the heat captured in other parts of the installation.
- Use methods of aeration of the slurry in the pits to promote aerobic conditions inside that favour the activity of bacteria that, during the decomposition of organic matter, do not produce odours as strong as anaerobic bacteria.
- Add chemical or biological additives to the slurry in the pit to reduce or neutralise the formation of odorous compounds, to fluidise it (facilitating its extraction), to inhibit the action of urease (an enzyme that causes the degradation of urea and subsequent emission of ammonia), or to acidify it (inhibiting the production of ammonia and the action of microorganisms and processes that generate foul-smelling gases). There is a wide range of additives of multiple types, so their use is an option as long as they have a justified and proven mechanism of action.
- Increase the height and speed of the exhaust of the air extracted from the ships to improve its dissipation.
- Place external barriers in warehouses, which create turbulence in the air outflow.
- Force and converge the air outlet of the buildings and pass it through a purifier that employs a humid filter (chemical or biological) to capture ammonia and other particles. Subsequently, a biofilter is passed with moist organic material, where all the volatile substances that generate foul odour are biologically degraded.
Tecnapur solid-liquid separator in operation. Photo: Rotecna.
Storage is the phase where we have the vast majority of the volume of slurry on our farms. Consequently, applying the appropriate mitigation techniques in this phase significantly impacts a more extended period and a more outstanding production of foul odours. The main measures we can take are the following:
- Reduce the dwell time and volume of stored slurry to the essential minimum, applying it to the field as soon as possible. To do this, it is essential to fertilise crops with different time windows of nutrient demand. An alternative is treating them as soon as possible, either on the farm or by sending them to a centralised treatment plant.
- Minimise the agitation of the slurry to the minimum necessary since doing so abruptly releases the gases retained in it and increases the production of odours.
- The separation of the liquid and solid phases of the slurry. Reducing organic matter in the liquid phase decreases the substrate for microbial activity, which minimises the production of volatile compounds; on the other hand, it allows us to compost the solid part, minimising the formation of smelly compounds by promoting aerobic decomposition.
- Reducing pH and adding acid to inhibit the production of ammonia, the action of microorganisms, and the processes that generate foul-smelling gases. This procedure is especially effective if applied to the liquid phase of the slurry once it has been separated since the more organic matter, the greater the amount of acid required due to its buffering effect.
- The use of covers, either encouraging the formation of a natural crust (the pond must be filled and emptied at the bottom) with floating elements or with a complete cover, which can be flexible or rigid.
- A complete cover will promote anaerobic digestion and the collection and use of the biogas produced. However, it will also significantly reduce hydrogen sulfide production and volatile fatty acids.
Finally, during the application of slurry to the field, especially if it is not treated, high levels of volatilisation and foul odours can be generated if the appropriate techniques are not used, such as:
- Avoid application in adverse weather conditions, high temperatures, and strong winds.
- Do not use application methods that encourage agitation of slurry, such as fan distribution: They should be distributed as close to the ground as possible, and the time for slurry to be incorporated into the soil should be minimised, if possible, by injecting it directly into the soil. Slurry separation improves the infiltration of the resulting solid phase, which is very important when applying slurry to grown crops or pastures, where it cannot be injected or buried by ploughing after application.
- When diluted in water, fertiliser should be applied to minimise the volatilisation of the foul-smelling elements.
Implementing these techniques can significantly help to reduce odour production, improve the perception of our farms and avoid conflicts that jeopardise the development of our activity and the future of our sector.