Blog
Blog>
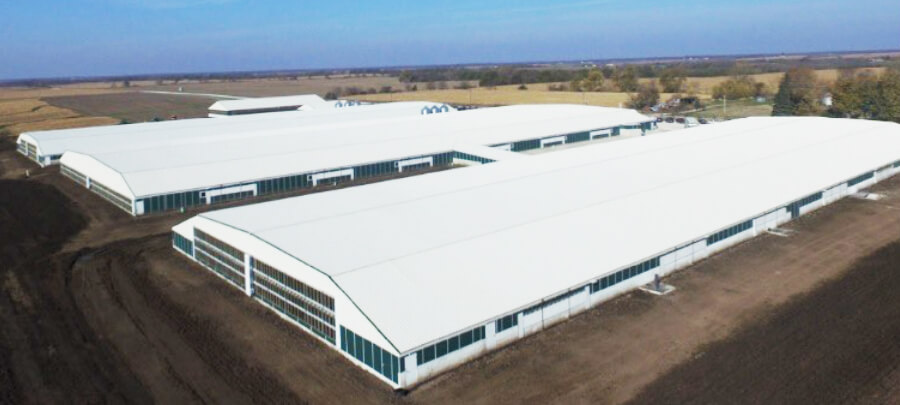
Environmental control on farms for a sustainable production
11th May 2023 - News
Having an environmental control system tailored to the specific conditions of each farm has a direct impact on animal welfare and productive performance. When environmental conditions are properly managed, with adequate air renewal, proper airflow, stable temperature, controlled humidity and acceptable gas levels, health issues decrease, average daily gain improves, and feed conversion efficiency increases. All of this ultimately leads to higher profitability for the farmer.
In addition to benefiting the animals, a well-balanced environment improves working conditions for staff and helps extend the service life of the facilities by avoiding condensation and corrosion problems.
Structural considerations and key parameters
The first step towards efficient environmental control is to understand the actual internal conditions of the barns. This requires an audit of both structural and functional elements that can affect ventilation and the ability to regulate the environment.
The orientation and location of the buildings are key, particularly in farms that rely on natural ventilation. Proper positioning can enhance airflow, whereas poor planning may hinder it. At the same time, accurate measurement of environmental parameters is essential, such as temperature, relative humidity, and gas concentrations like carbon dioxide (CO₂) and ammonia (NH₃). Temperature must remain within the comfort range according to the production stage and the animal’s weight, preventing stress and promoting optimal productive behaviour. CO₂ is a key indicator of ventilation efficiency; levels between 2,000 and 2,250 ppm are acceptable, but may increase in winter if minimum ventilation is poorly adjusted. Regarding NH₃, concentrations above 20–25 ppm can significantly increase the incidence of respiratory issues due to its irritating effects on the respiratory mucosa.
Challenging microclimates in critical production phases
In certain stages, such as farrowing, environmental control becomes especially complex. Two very different microclimates must coexist in the same space: sows require temperatures around 17 °C, while newborn piglets need a warm environment between 32 and 37 °C, free from drafts and cold surfaces.
Failing to effectively separate these microclimates can cause sows to reduce feed intake and milk production, while piglets may suffer from hypothermia, crushing, or inadequate colostrum intake. In fact, it is estimated that 70–80% of piglet mortalities occur within the first 72 hours after birth, with temperature being a key determinant in survival.
How a proper ventilation system should work
The environmental control system is based on drawing air from outside, conditioning it as needed (heating, cooling, or filtering it to prevent pathogen entry), distributing it evenly throughout the barn, and ensuring continuous air renewal to remove gases, dust and humidity.
Proper ventilation relies not only on the type of system used, but also on the condition of the facilities. Adequate thermal insulation, proper sizing, installation and calibration of every component, and an airtight structure (free of undesired air leaks) are essential for efficient climate control.
The objective is to avoid temperature fluctuations, prevent gas buildup (such as CO₂ and NH₃), and ensure a stable indoor environment. Poorly calibrated systems not only compromise animal welfare, but also lead to economic losses due to reduced performance and increased health-related costs.
Choosing the right ventilation system
The choice of ventilation system will depend on various factors, such as the climate, building design, geographical location, production type and level of farm automation.
Ventilation can be natural or mechanical. Natural ventilation relies on differences in air pressure (wind-driven) and air density (due to temperature differences). While this can be functional in mild climates, the main drawback is the inability to control the airflow volume, as it is fully dependent on external weather conditions. Conversely, mechanical ventilation systems allow for precise control of the internal environment. These systems use fans to move air through the barn and are classified based on how the incoming and outgoing air is managed.
Negative pressure systems are currently the most widely used in swine production. In these systems, fans extract stale air from the barn, creating a vacuum that draws fresh air in through controlled inlets. This method is energy-efficient, easy to regulate and provides precise airflow management.
Positive pressure systems push air into the barn using fans, while the air exits through strategically placed openings. These systems are useful in settings where external contamination must be avoided but require more careful control.
Neutral pressure systems combine inlet and exhaust fans to manage both air entry and removal. While offering high levels of environmental control, they are more energy-intensive and technically complex.
A comprehensive approach for effective environmental control
Beyond system choice, successful environmental control requires an integrated design tailored to each farm. A specific assessment should consider not only the type of animals housed, but also local climate, building orientation, degree of automation and the particular needs of each production stage.
Only through proper planning can a healthy, productive and sustainable environment be ensured for both animals and farm workers—maximising economic return while minimising health risks.